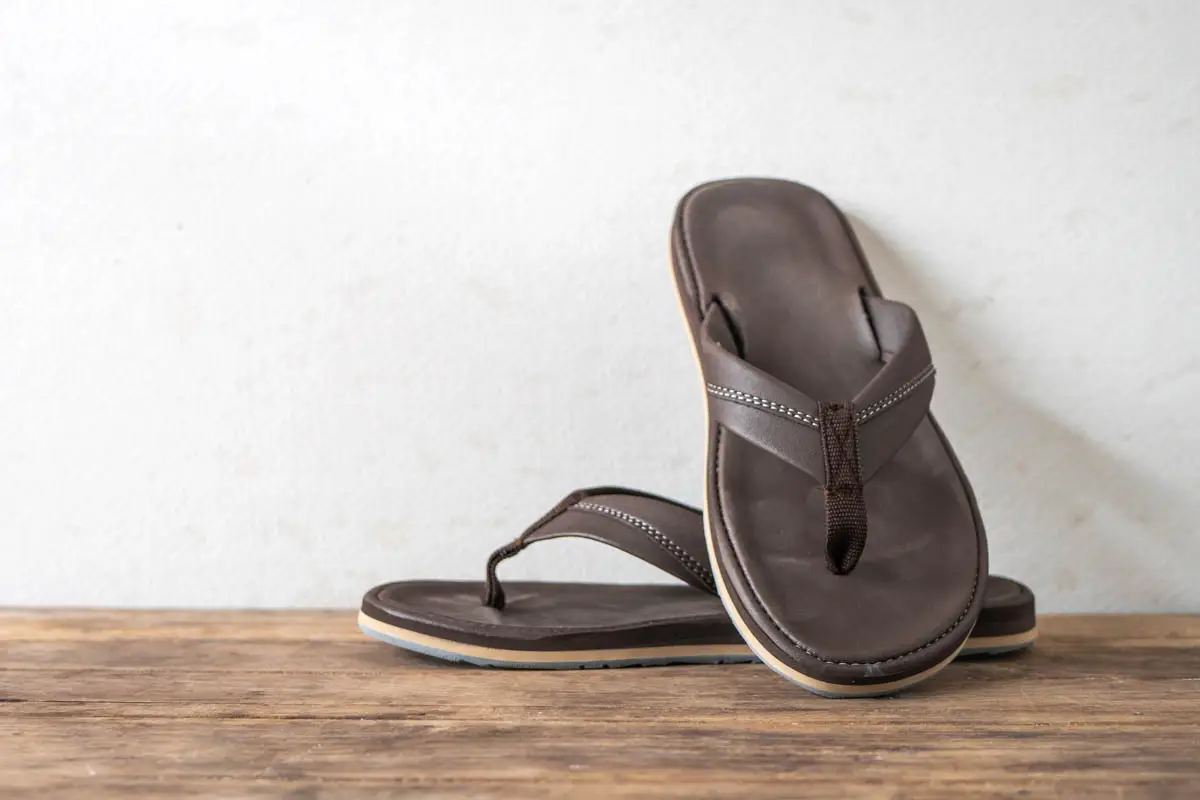
Challenge
The client, an European foot care brand with global retail distribution was looking to extend their product offering into footwear and sandals, leveraging a proprietary custom moulding innovation.
The client specifically wanted to introduce a distinguishing, innovative sandal that could be moulded to the customers foot in the retail shop, delivering a unique, high quality, personalized fit .
With deep experience manufacturing mouldable insole and foot care technology, Bestol was the ideal partner to help implement this technology.
The challenge facing the Bestol engineering team was to how to implement this proprietary moulding technology in an adjacent but completely new product line, with decidedly different manufacturing materials, processes, and tolerances.
This was going to require a cross-discipline team, working together to bring together materials that could meet the unique moulding requirements, while living up to the wearability expectations of the marketplace.
A considerable technical task was impregnating several thick material layers with a proprietary thermo-mouldable material, and assembling with a durable bottom material that could be moulded.
A rubberized material layer was common to premium beach sandals, but we found this was interfering with the moldability of this unique custom orthotic as rubber’s melting point was too high for other molded elements including the EVA midsole as well as the rigid arch system.
Having analyzed the construction problems, our engineers then turned their attention to more practical issues such as the choice of materials, the finishes and how to engineer a feasible, economical manufacturing.
Solution
After conducting a considerable amount of research and, and iterative testing and development, Bestol’s engineers arrived at a solution that involved switching Thermoplastic Rubber for a rigid, durable EVA sole allowing for aligned melting and moulding ranges with the other constituents.
While the EVA variant did not have quite the enduring wearability of TPR, it was light, mouldable and very comfortable.
Success
With their own innovative vision, strong manufacturer collaboration, and quality Bestol engineering, the client was able to introduce a unique new product that offered unmatched customization and comfort.
This new entry helped distinguish their brand in the competitive European summer footwear.